The Vibrapod Company
623 Hanley Industrial Court
St. Louis, MO 63144
Phone (314) 645-2900
Fax (314) 645-6700
|
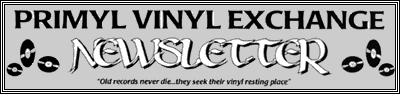
Volume 3,
Number 4 July - August 1998
Subscriptions
are $15 / six issues, $20 International
Primyl Vinyl
PO Box 67109
Chestnut Hill, MA 02167
Tel/Fax at (617) 739-3856
Email: pvx@ma.ultranet.com
|
Revenge
of the (Cheaper)
Pod People
Bruce Kinch |
If theres a single tweak genre that characterizes
the audiophile lifestyle, its got to be the $20 a foot category.
I dont mean size, of course, (although that does matter) but
the mind-boggling array of expensive balls, cones, pucks, spikes
and other widgets designed to be set under audio gear. There is
a "sound" reason for these gismos - the overweening audiophile
goal is to project the sound of the original performance into the
listening room, nothing less and nothing more. Unfortunately, audio
components (like everything else) resonate, or vibrate sympathetically,
with the reproduced sounds emanating from the speakers, as transmitted
through the air of floor, stands, racks, and cabinets. To make matters
worse, the motors and transformers in audio gear introduce additional,
non-musical vibrations into the arena, as do household appliances,
street traffic, and heavy footfalls. As we noted in our DIY pneumatic
turntable suspension article, the pickup stylus is essentially a
superbly sensitive vibration sensor, and most vinylists will give
this issue primary attention. However, other components notably
tube preamps, CD transports/players, and tape decks are also
subject to vibration/isolation treatment.
There are several categories of audio-feet. The first type is the
hard cone, initially designed for use under loudspeakers
the now familiar carpet-piercing spikes and the original
Tiptoes. Later applications included supporting equipment shelves
and components directly. Hard cones ideally have no compliance,
and mechanically couple (rather than isolate) an object securely
to the surface below. Thus hard cones should be used in sets of
three, as any surface irregularity will allow wobble if four or
more are used. The properties of hard cones vary with geometry and
materials (including aluminum, brass, steel, carbon fiber, ceramic,
and graphite). I tend to try hard cones under components which themselves
produce vibration, as the cones will "drain" the vibration
away to the larger supporting mass 9the shelf, stand, isolation
platform, or floor). Anything with a motor, transformer, or speaker
qualifies. In some cases, using marbles or ball bearings is worth
a try, as they allow horizontal compliance but not vertical movement.
For example, Wilson- Benesch uses small ball bearings between the
double plate glass shelves of their ultra-high-end turntable support
tables. (Primyl Tip: to keep the balls from rolling merrily
about, cut a hole in a small piece of foam (I use air conditioner
filters) thinner than the diameter of the spheres and stretch around
the ball.) Hard feet tend to affect the "speed", dynamics,
and clarity of the sonic reproduction.
A second category is the Tuned Footer. The reason hard cones
are made in so many different materials is that each substance has
its own resonance characteristics, which affect its performance.
Some footers are designed around these properties, to "tune"
the vibrating system. The famous Mpingo disks (the name is actually
an African term for a particular species of ebony) and Combak feet
are examples, as are the composite constrained layer damping Marigo
footers, and devices using springs or air bladders. There may be
both science and snake-oil at work here, but Ive heard some
strange claims validated experientially. Tuned footers can affect
the timbral and spatial characteristics of the sound, sometimes
making the presentation subtly more "natural".
The third category is the range of absorption/isolation products
employing high-tech materials like Sorbothane, Navcom, Norsorex,
or other rubbery polymer or low tech materials like sand
or lead shot. The Audioquest, Audio prism, and Deflex pucks, pods,
and (hemi)spheres are examples, as are Andy Barthas lead-and-caulk
Whatchamacallit muffins, Blue-Tak and Mortite, and Bright Stars
sand boxes (think of them as one big footer). The idea is that vibrations
cause the molecules or grains in these non-rigid substances to move
about on the microscopic level, converting the unwanted energy to
harmless heat. Being compliant, four or five (one in the middle)
may work better than three. Those seeds-in-a-balloon "Anti-stress"
squeeze balls are a favorite cheapo alternative. Absorptive footers
tend to smooth out the sonic signature, in my experience.
All the above are worth exploring, but the foregoing has mostly
been by way of introduction of a new isolation product the
Vibrapod which uniquely has aspects of all three categories
in its design. Its also the product of serendipity, and therein
lies an interesting tale. Sam Kennard, the manufacturer, is a Primyl
Vinyl subscriber and a way-serious audiophile. He owns a company
in St. Louis that makes various sub-contracted plasticky doohickeys,
and he treats his employees (and himself) to a higher standard of
workplace music reproduction than many might have at home. Hell,
hes even hired ex-audiostore employees to work there. So one
day he notices that the shops CD player, which sits atop some
machinery, is skipping whenever the big oven operates. On impulse,
he sticks a couple of the widgets or whatever its making under
the player and audeus ex machina the things
plays flawlessly. Thus began the development of the Vibrapod, several
iterations of which hes sent to us to evaluate, and which
now has become a real product.
The Vibrapod is a 2.5" plasticky doohickey itself, of a shape
thats hard to describe, so the pictures may help. As with
cones and balls, the geometry is important here
the component is supported by the 1 ½" dia. Top ring, although
in cross-section this is revealed to be an arch, a structure with
interesting load bearing/transfer characteristics (which is why
they call it architecture, not pillaristics or wallology). The inner
edge of the thin walled circular arch is supported by a vertical
cylinder of somewhat thicker dimensions, the outer edge buttressed
(sorry) by a much heavier, sloping ring i.e. an asymmetrical
arrangement. The inner cylinder has a floor with a small hole to
facilitate attaching it. The top ring, being thin, flexes under
load, much as a radial tire is designed to bulge as it meets the
pavement. And like a tire, the Vibrapod is tuned the
instructions suggest using one Vibrapod per 2.625 lbs. or so of
load (or 1.2kg, if you are into metric). They also suggest placing
them around the periphery of the shelf or component to be supported,
not the middle, but one can feel free to experiment the things
are dirt cheap by audio standards, at just $6 apiece. The tuned
flexing is part of the system, as the soft plastic also absorbs
energy but since the plasticizers can affect adjacent surfaces,
Kennard suggests protecting vulnerable finishes with sheets of inexpensive
stationary store acetate.
Ive had a lot of fun with the Vibrapods. The hole in the
base made for easy direct fixing to several components like the
tape deck and phonostage. For items needing more ground clearance,
the holes allow combining two back-to-back with a small nut and
bolt I used steel fender and/or neoprene washer in between
to add stability. I also tried stacking plate glass/pod/glass/pod
sandwiches to put under a component (Manapods?) as well as simply
putting them in place of feet. I used a bunch around the periphery
and three near the bearing of my Well-Tempered (leaving the motor
assembly sitting directly on the marble base I have under the turntable.
So, do they work? Yes, but like any of these tweaky things, the
audible effects vary from one component to another, but are reliably
cumulative. I find the Vibrapods make the overall presentation slightly
more "relaxed", dimensional, and less fatiguing
exactly what the expensive ones are designed to do. But youd
have to try them under your own components, in your system, and
make your own call. Different feet=different sound. Bottom line
for me is I can put them under all sorts of things I could never
justify using the $20 per foot variety. The tape deck, tuner, DAC
and jitterbox, stepup transformer, even the power conditioner can
now all get the same attention as the preamp and source components.
Jeff Bellin has also tried out some Vibrapods, and provided Primyl
Vinyl his own assessment:
An audiophile friend of mine and I recently got
to do a good A/B-ing of the Vibrapod isolation pods. I'm relatively
new to audiophiledom but I've had 30 years of musicianship behind
me, so my ears are audiophile quality! My friend has been in the
audio business in a mid to high end hi-fi store for about 20 years,
so I thought between the two of us we'd be able to articulate the
differences, if any, the Vibrapods made. I had already played
with Vibrapods underneath my inexpensive CD player and discovered
quite an improvement (increased spaciousness, better defined). I'd
been running my turntable with the 'pods under it for a couple of
weeks, and wanted to make a real test of the set-up (a VPI HW-19
jr with the Mk III platter; a Morch UP-4 tonearm/Sumiko Blue Point
cartridge; a Cyrus II integrated amp and Magnepan SMGc speakers
completed the rig).
We played a variety of music, from Dylan's new "Time
Out of Mind," and The Beatles' "Magical Mystery Tour"
and "Please Please Me" albums, to the Classic Records
reissues of Miles Davis' "Kind of Blue", and even the
Reiner/Respighi "Pines of Rome." After about an hour and
a half a listening, we decided to remove all the Vibrapods. (I have
16 pods sitting underneath a 1/2 inch MDF board on which the turntable
sits.)
This, by the way, was the first time my friend had
heard my VPI tables, so he was checking this out too. He's a big
Dylan fan, and "TOoM" is a well recorded album so we decided
that would be the first comparison. Interestingly, his first reaction
was that is was more musical without the Vibrapods. I asked
him what was "more musical", but he couldn't immediately
put his finger on it. I heard, on the other hand, a more confused
soundstage, less depth, less air around the instruments without
the Vibrapods. I suggested we move right back to using the 'pods
to make an immediate comparison. (It's always better to do an A/B/A
rather than just A/B in order to make sure what you heard is, indeed,
what you heard. Sometimes any difference seems like an improvement,
just because it's a difference). Surprise: he now liked it with
the Vibrapods much better, and so did I - MUCH improved soundstage,
the air around the instruments had returned, everything was much
more defined. An enormous sonic improvement, at least as much sonic
improvement as I got going from a $29 MIT 6 cable to a $400 Audioquest
Emerald on my CD player.
|
|
|
Awards
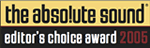
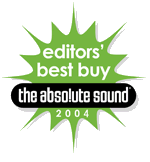
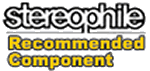
Since October 1998
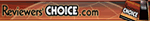

|